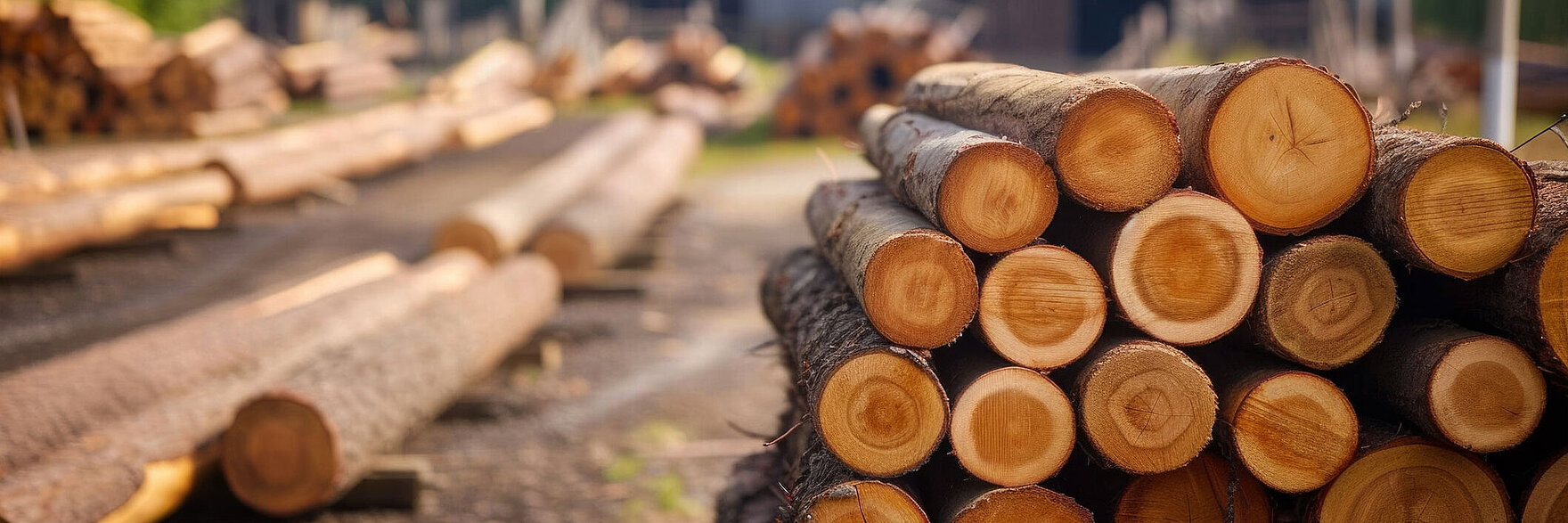
Effective log cutting
Wood is a unique and sustainable material that differs significantly from others. Various factors must be taken into account to achieve optimum cutting results and maximum bandsaw blade life. Operators of stationary and mobile band sawmills need to know the type of wood and its characteristics in order to select the appropriate band saw blade and set the right cutting parameters.
To a large extent, the choice of the right tool is simplified by the versatility of the GENERO band saw. The geometry, developed and tested over a long period of time, together with extreme manufacturing precision and modern processes, gives you a competitive advantage in cutting efficiency.
Influence of wood properties on cutting
Different types of wood differ in material structure and hardness. Wood is also subject to growing conditions and environmental influences that affect the possibilities of use. In addition, heavily soiled bark, metal inclusions or frozen wood can place special demands on the machine operator and the bandsaw blades used.
When cutting softwood and hardwood, the following properties and characteristics must be taken into account in addition to the type of wood:
Required moisture content for different types of wood | |
---|---|
Tolerance range | Application |
15-20% | Exterior application |
15-20% | Construction wood |
14-18% | Dry for loading |
12-15% | Windows, exterior doors |
10-18% | Planed products |
10-13% | Glued laminated wood |
6-10% | Furniture in heated rooms |
6-8% | Parquet wood, veneers, musical instruments |
Digital hygrometer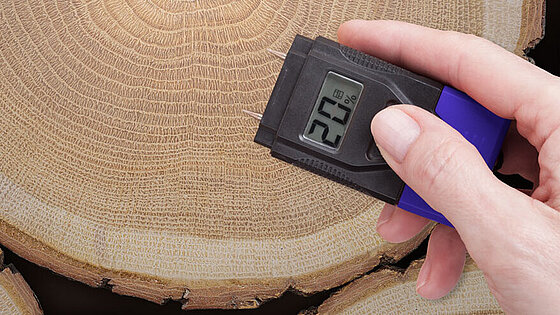
To determine the moisture content of the wood, we recommend using an electronic moisture meter, which:
- measures the resistance or electrical capacitance of wood,
- allows quick and easy determination of moisture,
- especially suitable for sawn timber and fresh logs.
Check wood moisture for optimum cutting results | |
---|---|
Characteristics | Recommendations |
Wood with a high moisture content (above approx. 30%) is softer and results in lower cutting forces. High moisture content can also cause the sawdust to stick together faster and clog the spaces between the teeth of the bandsaw blade. This can lead to poor sawdust removal, heat generation and increased friction. | For wet wood, an aggressive tooth geometry with large gullet area is recommended to prevent sawdust from sticking and clogging. Reduced cutting speed helps minimize clogging the gullet area of the bandsaw blade, while a slower feed rate ensures a clean cut. |
Wood with a low moisture content (below approx. 20%), especially hard dry wood, can dull the teeth of the bandsaw blade more quickly due to its high density and abrasiveness. | Smaller tooth pitch reduces stress on the bandsaw blade and reduces resistance when cutting dry wood. Increased cutting speed helps prevent heat build-up, while a properly selected feed rate reduces the risk of cracking. As dry wood is more abrasive, the bandsaw blade should be checked regularly to detect excessive wear early. |
Cutting wood with different densities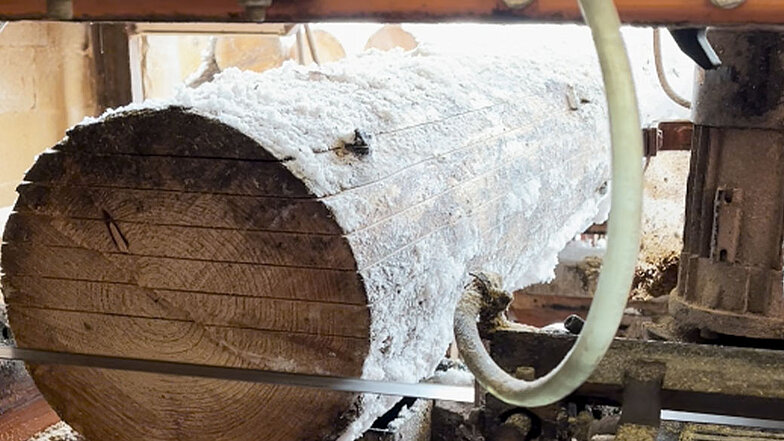
Cutting wood with different densities (e.g. softwood with thick and hard knots) is always a challenge for the bandsaw blade, the machine and the operator. Not only must attention be paid to the geometry of the bandsaw blade, especially the tooth rake angle, to ensure that it is properly matched to the type of wood, but also the feed rate setting must be adjusted for optimum results.
Frozen or partially frozen wood
Processing frozen, especially partially frozen wood presents a special challenge. This is because it has different densities, which makes it even more difficult to cut. In general, a less aggressive tooth rake angle of 7° can be recommended for normal cutting of frozen wood instead of the universal 10°. Or use more durable bandsaw blades.
Use bimetal bandsaw blades
For cutting wood with different densities, we recommend using a precise bandsaw blade such as GENERO, which is suitable for cutting softer, harder or frozen wood due to its particularly high hardness and toughness. Thanks to the versatility of bimetallic bandsaw blades, you will achieve a longer service life, greater efficiency thanks to less frequent replacements and less need for sharpening with skipping the resetting step.
Effect of log diameter on sawability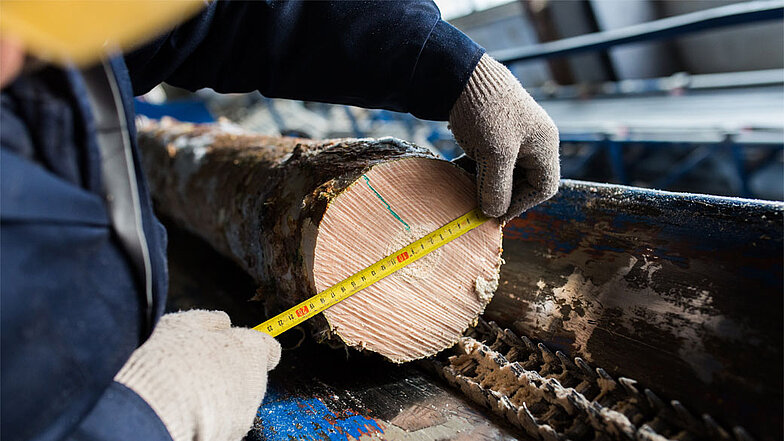
The diameter of the log affects the performance of the machine, the cutting resistance and the wear of the bandsaw blade. Large logs provide more stability when cutting, but increase cutting resistance and generate heat. It is therefore recommended to choose a larger tooth pitch, adjust the feed rate and take care of efficient cooling. In contrast, small logs are easier to cut, but may slip or vibrate when cutting. A stable clamping and a smaller tooth pitch of the saw blade are therefore necessary.
Choosing the toothpitch for log bandsaw blades | |
---|---|
Cut length in mm | Number of teeth per inch (tpi) / Tooth pitch (mm) |
40 - 200 | 2 tpi / 13 mm |
200 - 800 | 1,15 tpi / 22,22 mm |
800 - 1400 | 0,8 tpi / 31,75 mm |
Cutting resin-rich wood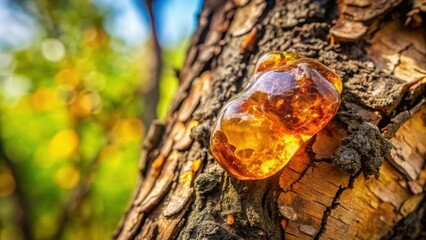
All types of wood emit resin during processing. However, some types of wood, such as spruce, larch or pine, are particularly rich in resin. When cutting, make sure that the machine remains clean and blow it out regularly, otherwise it is difficult to achieve precise cuts. Regular cleaning of the bandsaw blade prevents further resin build-up and excessive wear.
Less resin adhesion is also achieved by using the GENERO bimetal bandsaw blade, which has a particularly fine blasted surface with a smooth finish.
![]() BranchesHeavily knotted wood is more difficult to cut than wood with few knots. | ![]() Spiral growthStrong spiral growth can cause deformation of the wood when cutting. |
---|---|
![]() CracksCracks and gaps can cause the wood to splinter or break during cutting. | ![]() DiscolorationSigns of wood damage, such as blue stain, fungal infestation and rot, can sometimes affect the strength of the wood and thus the cutting result. |
Effect of inclusions on the blade life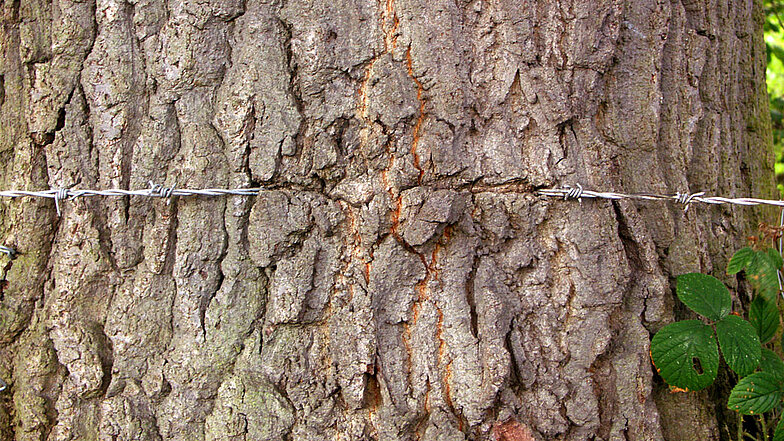
While bark contamination with dirt or stones can be dealt with in most cases by a debarker, other inclusions, which can be metal, are difficult to detect. These foreign bodies have a significant effect on the life of bandsaw blades, causing premature wear of the teeth - dulling of the bandsaw blade. The GENERO bimetal bandsaw blade with alloy steel backing material and teeth made of high speed steel (HSS) provides a long service life in spite of the inclusions.
Examples of metal parts in wood:
- fencing of pastures that are ingrown in wood,
- bite protection bars or wires used to guard trees,
- nails or screws in trees that can penetrate deep into the wood.
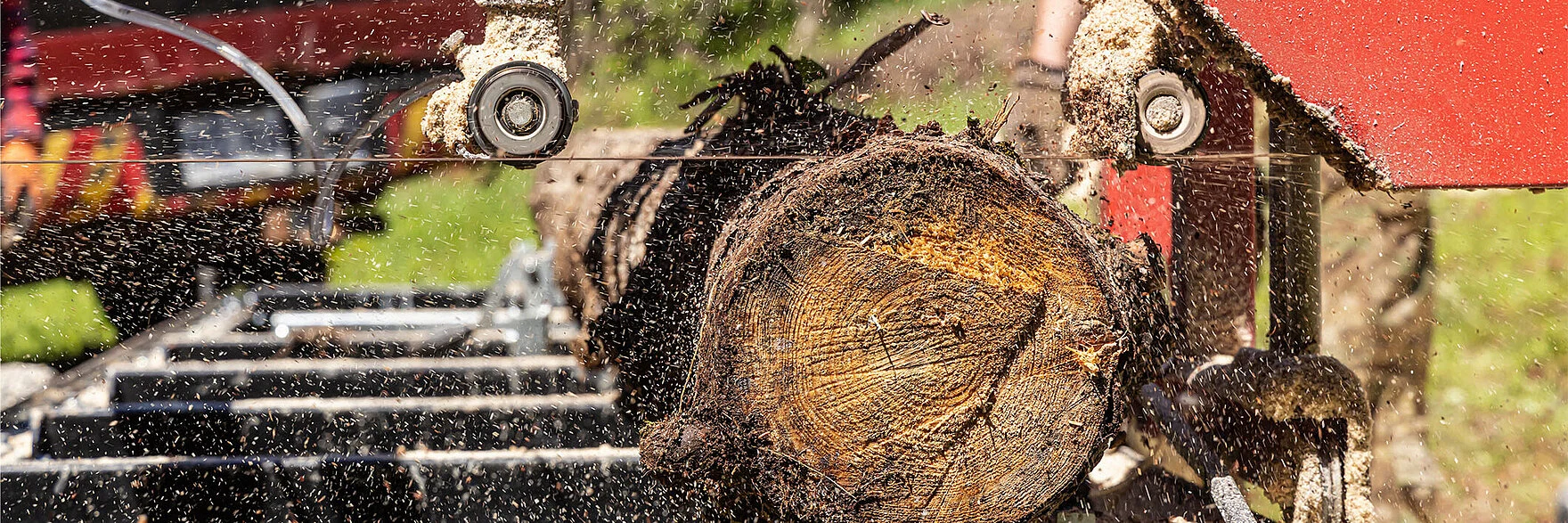
Bandsaw blades for cutting wood: Tips for use
Whether you use mobile or stationary saws to make beams, battens or beams, the following tips will make your job easier, increase productivity and extend the life of your bandsaw blades. But please keep in mind that there is no universal machine setting when cutting wood, and even when processing the same type of wood, additional machine adjustments may still be needed.
Prefer blades with tooth protection on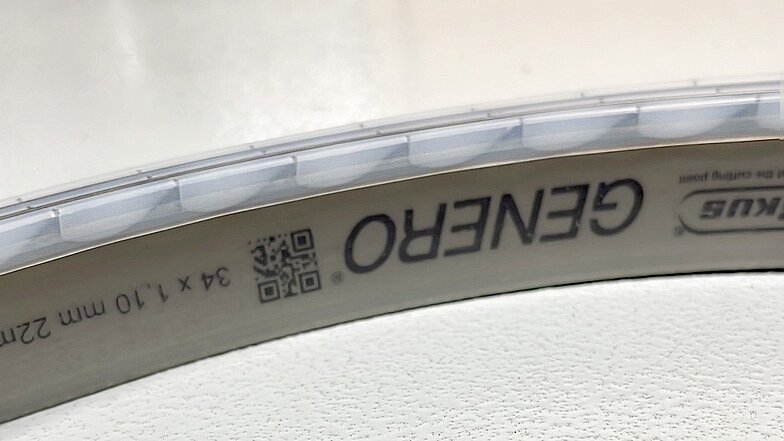
This is not obvious, but tooth protection can significantly help to protect the teeth not only against mechanical damage, but also partially against corrosion on the most stressed parts of the bandsaw blade. The plastic tooth protection can be used repeatedly each time the saw blade is re-hung or reground. Re-installation is easier with the mounting aid developed by WIKUS.
The plastic tooth protection is also very important in the prevention of work accidents when handling bandsaw blades. Sharp teeth can cause painful injury, so always remove the protection only after it has been properly positioned on the impellers, in the guides and after the bandsaw blade has been tensioned.
Let the bandsaw blades rest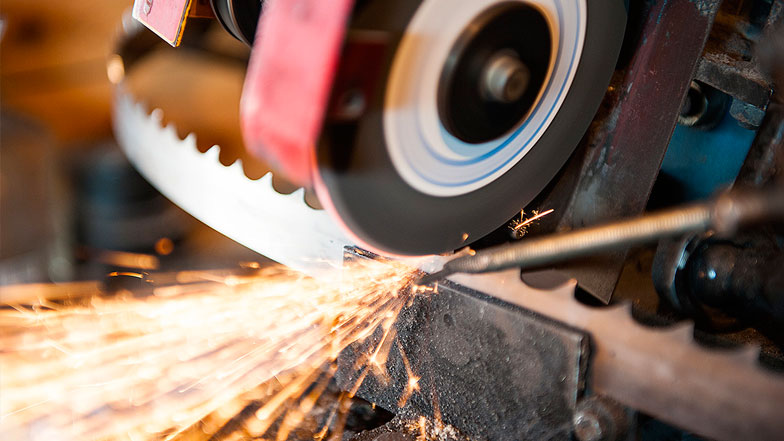
Compared to conventional saw blades, bimetal bandsaw blades last twice as long. Nevertheless, it is recommended to take them off after 2-4 hours of cutting and let them rest for another 8 hours. The bandsaw blades are subjected to high temperatures and high tension during cutting, which prolong them. Therefore, hanging them up will prevent cracks from forming. After the bandsaw blade has rested, it can be resharpened and put back on the bandsaw machine.
Resharpen bandsaw blades
In purely practical terms, if you have a feed rate of e.g. 0,1 m/s, you will cut approximately 360 m per hour of operation, which is 1440 m in 4 hours of work. With a trunk length of 5 m and 20 cuts per trunk, you will achieve a total of 288 cuts. You can therefore fully cut up to 15 logs before the bandsaw has to be resharpened. Each sharpening takes approximately 0,1 mm and you can sharpen 10 times, which is up to twice as much as conventional log band saw blades.
Regular maintenance of impellers
For optimum cutting results, the impellers should be checked regularly for cleanliness and wear and their cork or rubber coating should be replaced if necessary. This prevents the steel part of the impeller from coming into direct contact with the bandsaw blade, thus achieving a longer service life. If this coating is worn, the impellers are usually repaired at the same time. In the event of uneven wear over time, the driven impeller can also be replaced with the drive impeller, where this layer is usually more stressed.
Position of the bandsaw blade on impellers
The position of the bandsaw blade on the impellers must also be correctly adjusted and checked. The teeth of the bandsaw blade should extend in front of the contact surface of the impeller to prevent damage to both the impeller and the bandsaw blade. The base of the teeth should extend approximately 3-4 mm in front of the impeller.
Check the bandsaw blade guides regularly
Precise and trouble-free cutting is only possible with a correctly adjusted bandsaw blade guides according to the machine manufacturer's specifications. Most often the guides consist of rollers, which ensure the correct position in relation to the machine base and stability in the cut. Their technical condition and adjustment must be checked regularly. If they are worn in any way (conical shape, worn flange, damaged bearings), they must be replaced to avoid unwanted vibrations and cracking of the bandsaw blades.
How to adjust the rollers
The adjustment of the rollers is carried out after the bandsaw blade has been fitted and tensioned. The horizontal and vertical inclination is monitored to ensure that the bandsaw blade is guided correctly. The rollers should be approximately 1,5-4 mm from the back of the bandsaw blade. The flanges serve as a support in the cut to achieve greater accuracy, but permanent contact damages both the rolls and the bandsaw blade.
On most machines, the position of the rollers is set lower than the axis of the lower edges of the impellers. This results in additional belt tension, reduced vibration and more accurate cutting. The downward adjustment varies according to the machine manufacturer, typically in the range of 3-6 mm.
Cooling and cleaning the wood bandsaw blade
The bandsaw blade is normally rinsed with water to ensure effective cooling during use. It also cleans the tool and reduces friction, which ensures more accurate cutting and a longer life of the bandsaw blade. Cleaning additives can only further improve the result.
Cutting wood in frosty conditions
If you are cutting frozen wood, antifreeze can be added to the water and flushing agent tank to provide:
- prevents the water in the tank from freezing,
- ensures better lubrication of the bandsaw blade,
- improves gliding properties by reducing friction and wear,
- leads to cleaner cuts
- and extends the life of the bandsaw blade.
Optimum tension of the wood bandsaw blade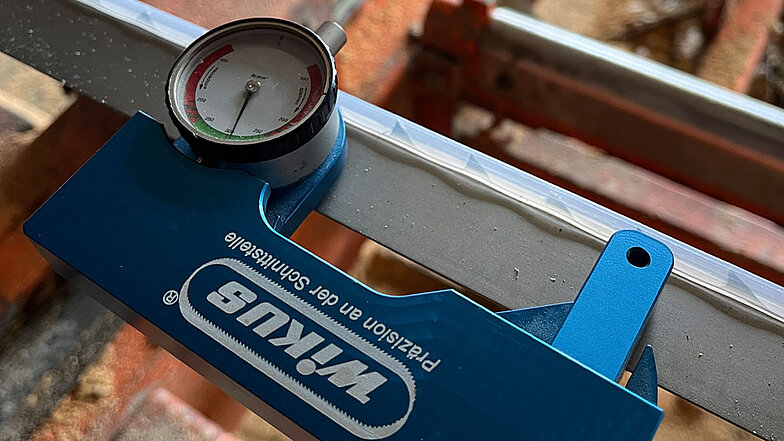
Precise cuts are only possible with the correct tension of the bandsaw blade. The tension of the bandsaw blade must be checked regularly, even during use, as it heats up during cutting. This leads to a slight stretching of the material, lowering the tension and can result in uneven cuts.
The recommended tension for our GENERO bimetal bandsaw blade for woodworking is 250 - 300 N/mm².
Cutting speed setting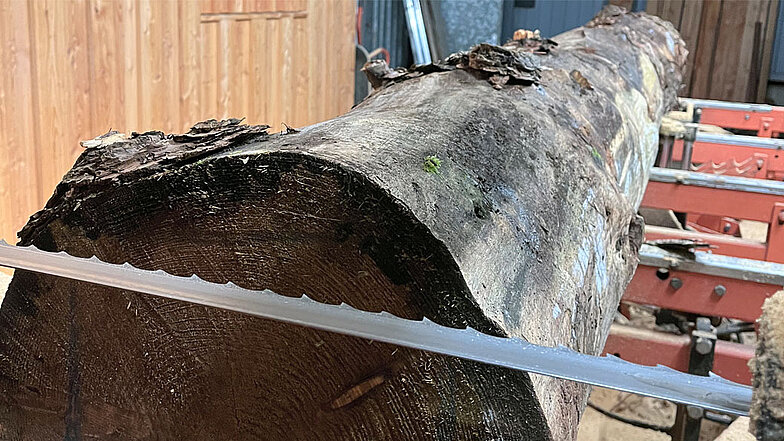
The cutting speed must be adjusted individually according to the type of wood and also to the contamination of the bark or trunk. Even with a new bandsaw blade, the cutting speed must be adjusted accordingly. Setting the correct speed, usually between 1050 and 1650 m/min, prevents overheating and achieves optimum performance.
When cutting frozen wood, we recommend not to exceed a speed of 1450 m/min.
Optimum feed rate
For the best cutting results and maximum life of the bandsaw blade, it is necessary to select the appropriate feed rate according to the type and condition of the wood.
Wood types differ fundamentally in their density. Particular attention should be paid to softer woods, as density can change more frequently, especially in areas with knots. The cutting feed rate should therefore be checked regularly and adjusted if necessary. Because harder woods have a more uniform density, they can be cut with a higher and smoother feed rate.
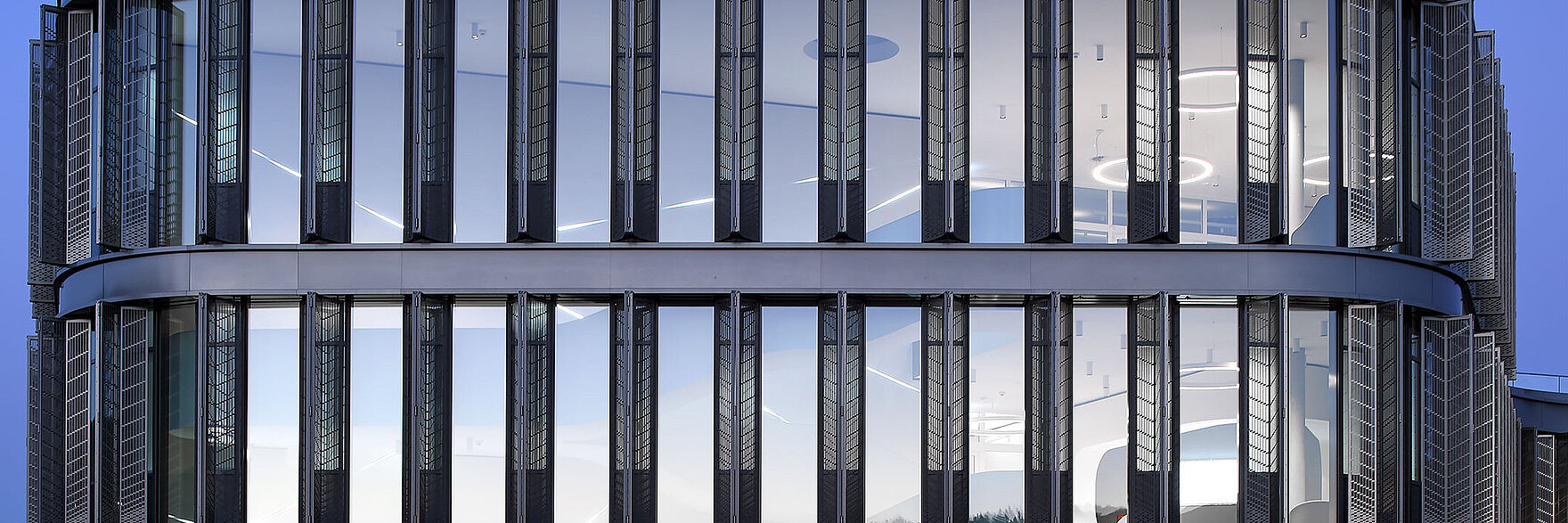
Introduction
The WIKUS brand is synonymous worldwide with maximum precision, quality and performance. Manufactured using only first-class materials, it uses state-of-the-art production processes with strict quality control at every step.
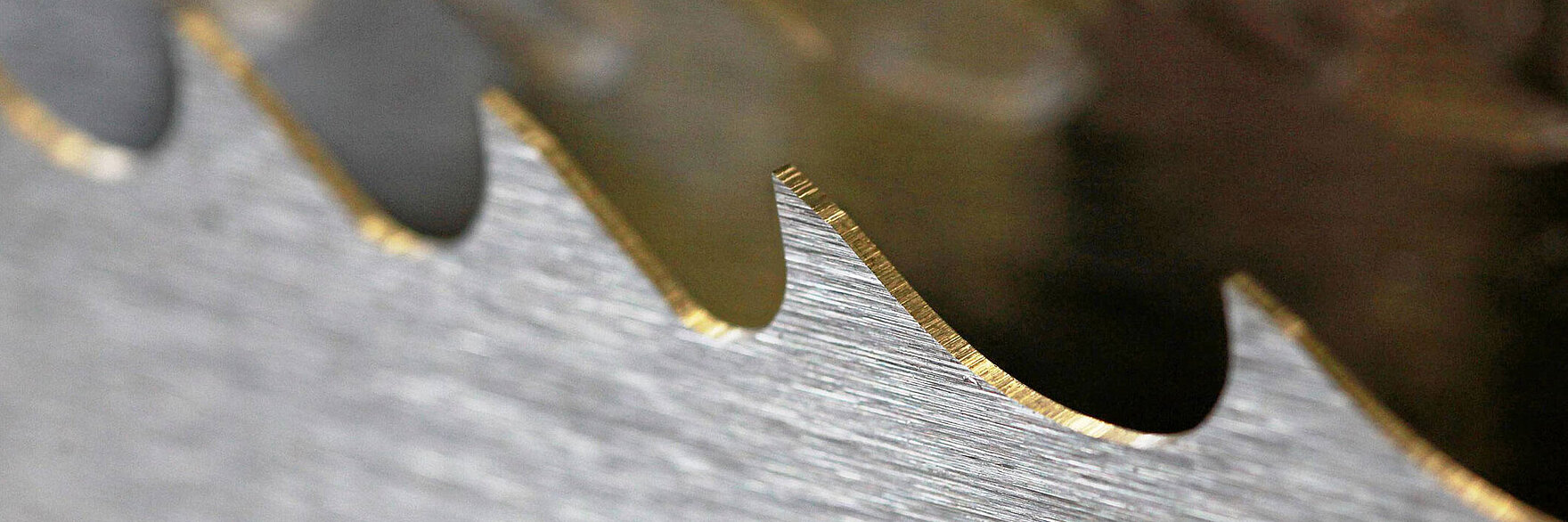
Why WIKUS
Because thanks to continuous innovation, our band saw blades meet the most demanding requirements for every application, not only in industry, and are known worldwide for their precision, durability and maximum performance.

Contact
No matter whether your operation is located in Prague, Bratislava or anywhere else, we have an expert technician on hand who is always ready to help you. Contact us and together we will find a solution.